Lightweight Medical Device Housing: Enhanced Performance Through Innovation
Learn how we helped a leading medical device manufacturer reduce their device housing weight by 22% while improving impact resistance and maintaining FDA compliance.
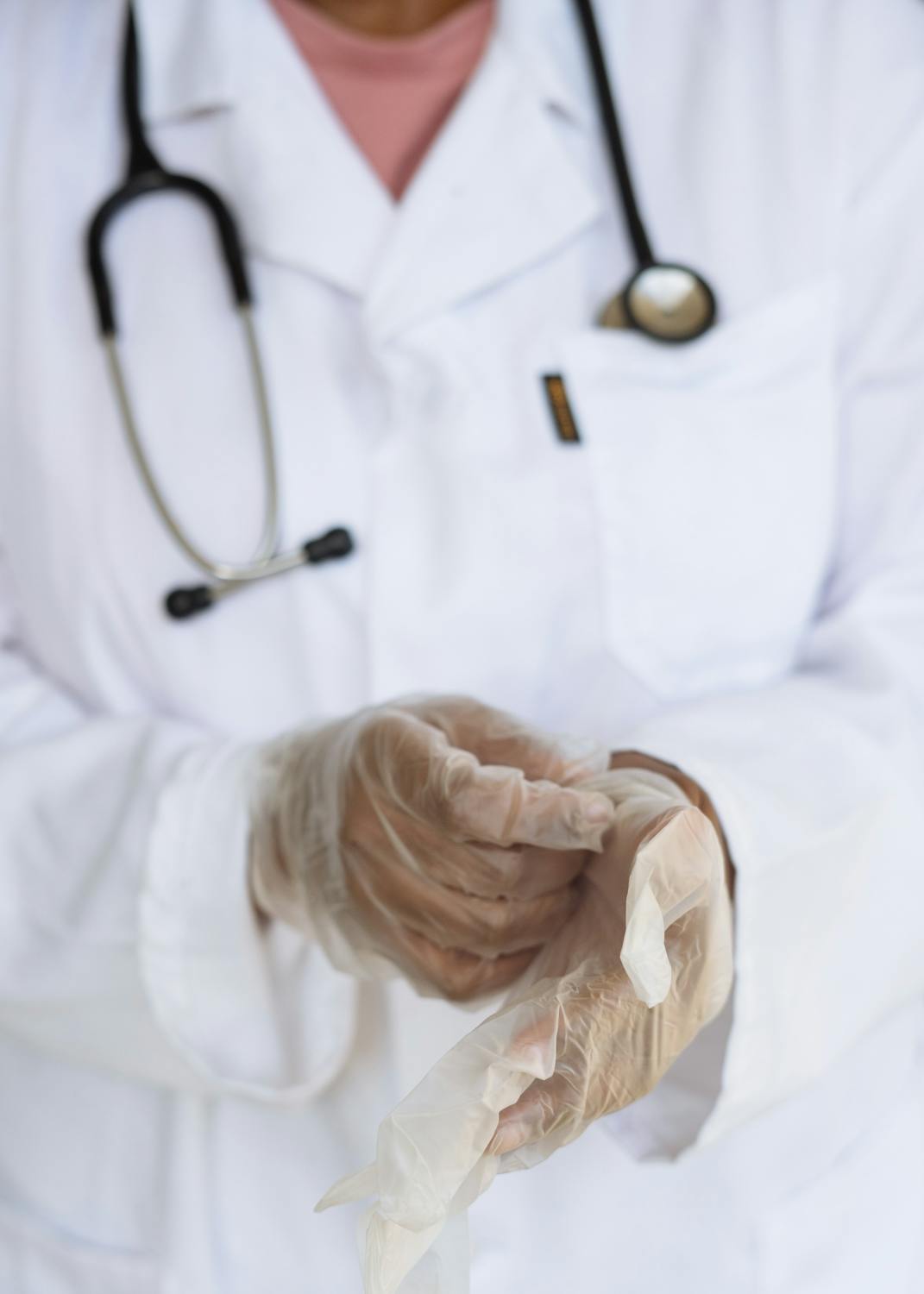
Key Achievements
22%
Weight Reduction
Lighter than original design
45%
Impact Resistance
Improvement in drop test performance
18%
Cost Reduction
Manufacturing cost savings
3
Time to Market
Months from concept to production
The Challenge
Our client needed to reduce the weight of their portable medical device housing while maintaining impact resistance and meeting strict FDA requirements. The existing design was causing user fatigue and had occasional failures during drop testing.
- Required 20% weight reduction target
- Needed to maintain or improve impact resistance
- Must meet FDA and ISO 10993 requirements
- Cost reduction goals for high-volume production
Our Approach

We employed a comprehensive approach combining advanced materials science, structural analysis, and innovative design techniques:
- Conducted extensive FEA simulations for optimization
- Evaluated multiple material options through testing
- Used topology optimization for weight reduction
- Implemented Design for Manufacturing (DFM) principles
The Solution
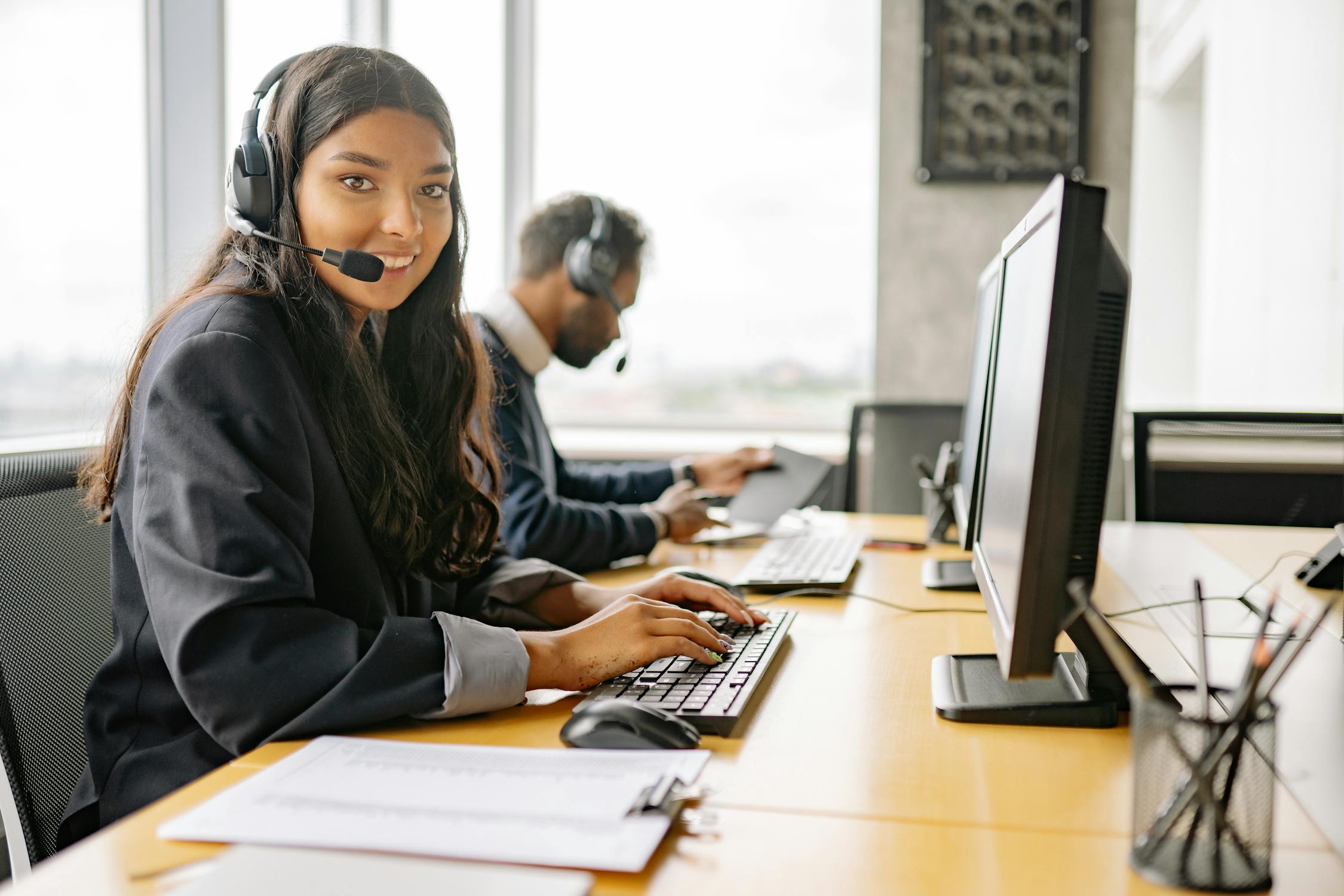
Our solution incorporated several innovative features:
- Optimized rib structure for maximum strength-to-weight ratio
- Custom PC/ABS blend with enhanced impact properties
- Integrated mounting features to reduce assembly time
- Textured surfaces for improved grip and aesthetics
Results & Impact
The new design exceeded all project objectives and received overwhelmingly positive feedback from end users. Key achievements included:
- 22% reduction in overall weight
- 45% improvement in impact resistance
- 18% reduction in manufacturing costs
- Zero field failures reported since launch
- Successful FDA and ISO 10993 certification
"ATI Engineers' innovative approach to our device housing redesign exceeded our expectations. The significant weight reduction and improved durability have received outstanding feedback from our medical staff users."
Technical Specifications
Detailed specifications of the final design
- Material
- Medical Grade PC/ABS Blend
- Wall Thickness
- 1.8mm - 2.2mm
- Surface Finish
- SPI-A2 (16-24 μin)
- Color
- RAL 9003 Signal White
- Impact Rating
- IK08 (5J Impact)
- IP Rating
- IP54 (Dust/Splash Protected)
- Flammability
- UL94 V-0 Rated
- Biocompatibility
- ISO 10993-5, -10 Compliant
Ready to Optimize Your Design?
Let's discuss how we can help improve your medical device design.
Related Case Studies
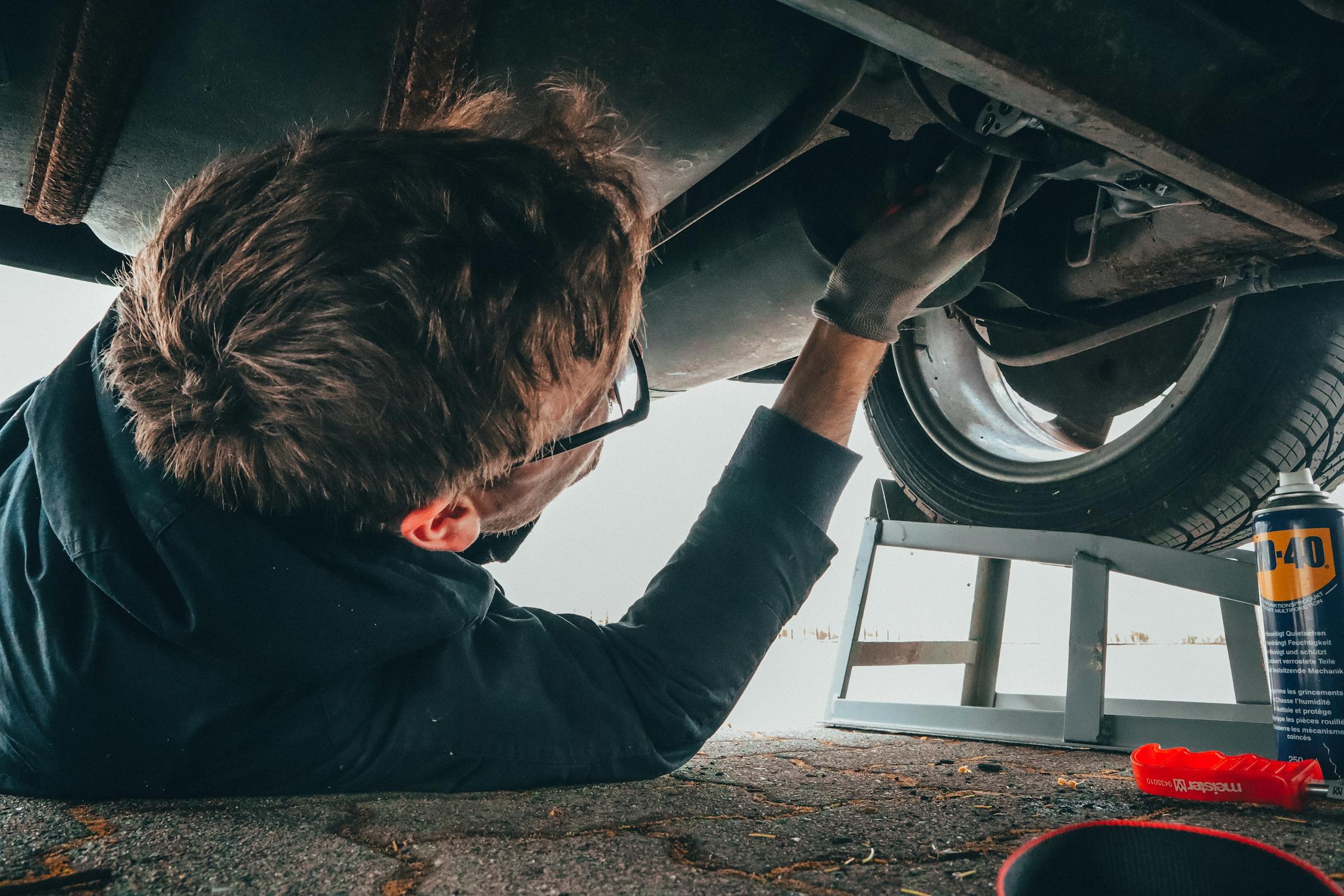
Automotive Connector Assembly
Streamlined assembly process for complex automotive connector
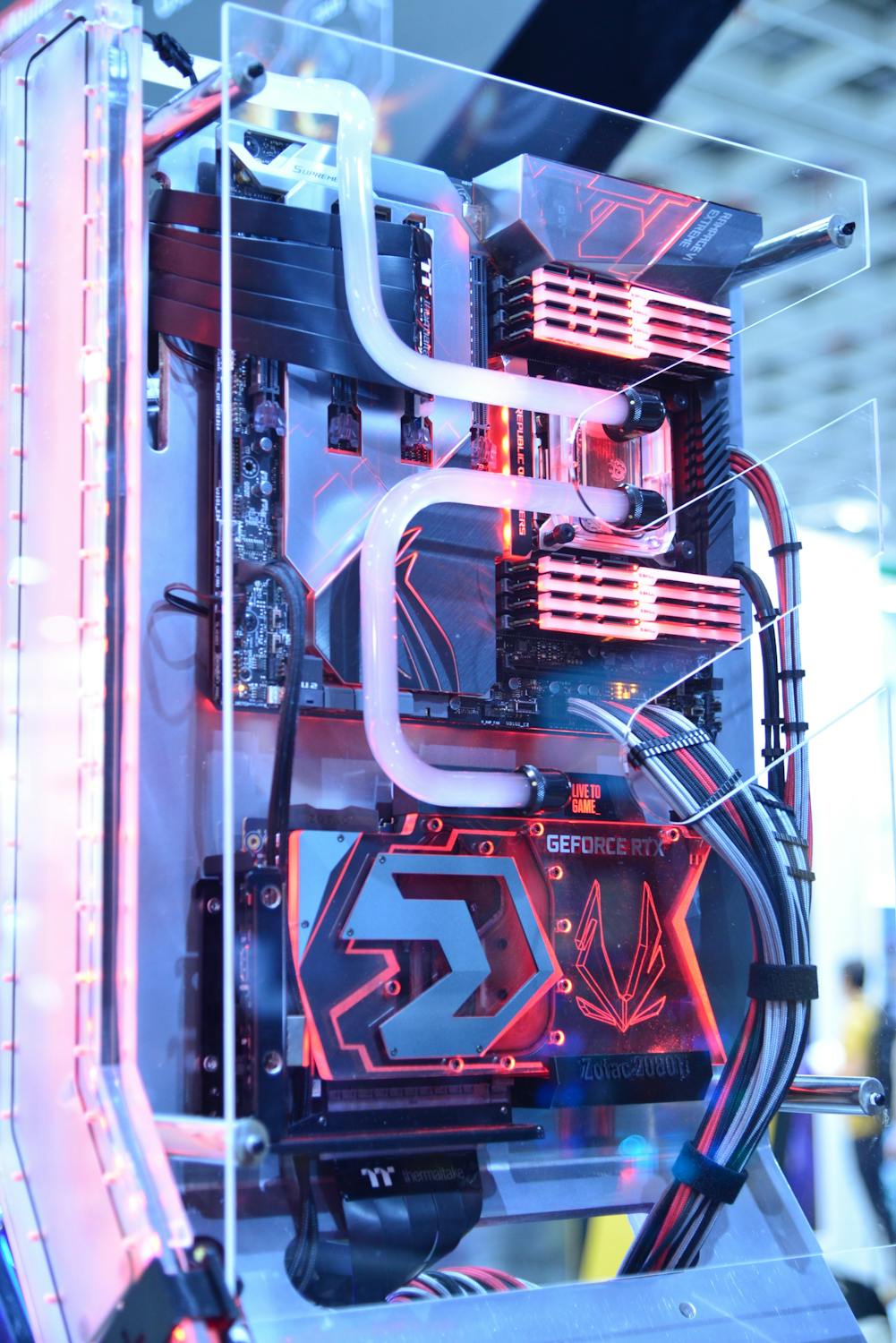
Consumer Electronics Enclosure
Water-resistant housing design for consumer electronics