Optimizing Thermal Management in Industrial Equipment Housing
Learn how we helped a leading industrial equipment manufacturer reduce operating temperatures by 15°C and extend service life through innovative thermal management solutions.
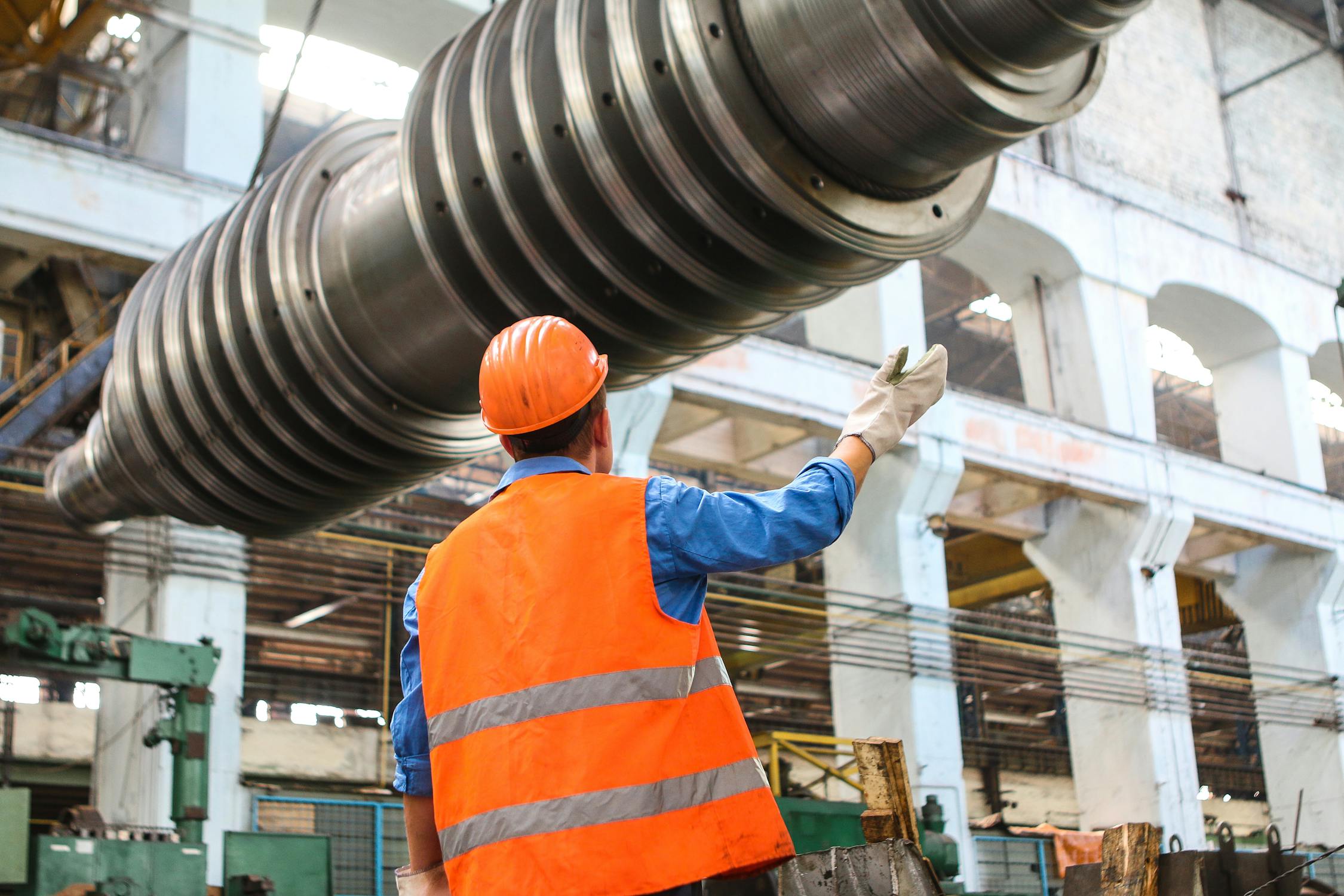
Key Achievements
15°C
Temperature Reduction
Lower operating temperature
40%
Service Life
Extended equipment lifespan
25%
Assembly Time
Reduction in assembly time
90%
Warranty Claims
Decrease in warranty issues
Client Overview
Our client, a leading manufacturer of industrial power conversion equipment, needed to address thermal management challenges in their next-generation frequency converter housing. The equipment operates in harsh industrial environments with ambient temperatures up to 40°C while generating significant internal heat from power electronics.
Initial Challenges
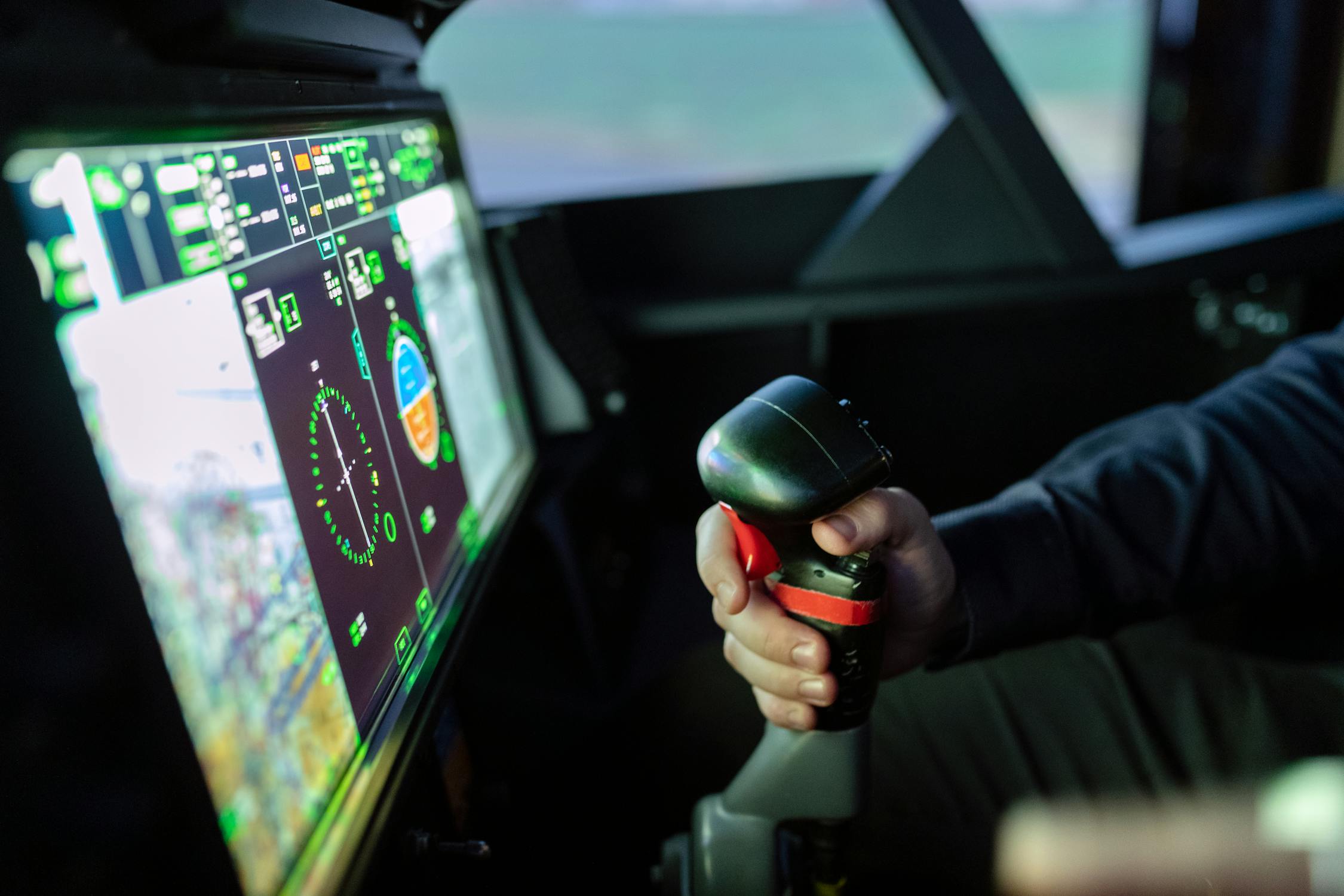
Thermal Management Issues
- Internal temperatures exceeding component specifications
- Uneven heat distribution causing thermal stress
- Insufficient natural convection cooling
- Limited space for traditional cooling solutions
Environmental Factors
- High ambient temperatures in industrial settings
- Exposure to dust and moisture
- Vibration and mechanical stress
- 24/7 operation requirements
Operational Constraints
- Maintain IP66 and NEMA 4X ratings
- Cost-effective solution for high-volume production
- Minimize maintenance requirements
- Retrofit compatibility with existing installations
Technical Solution
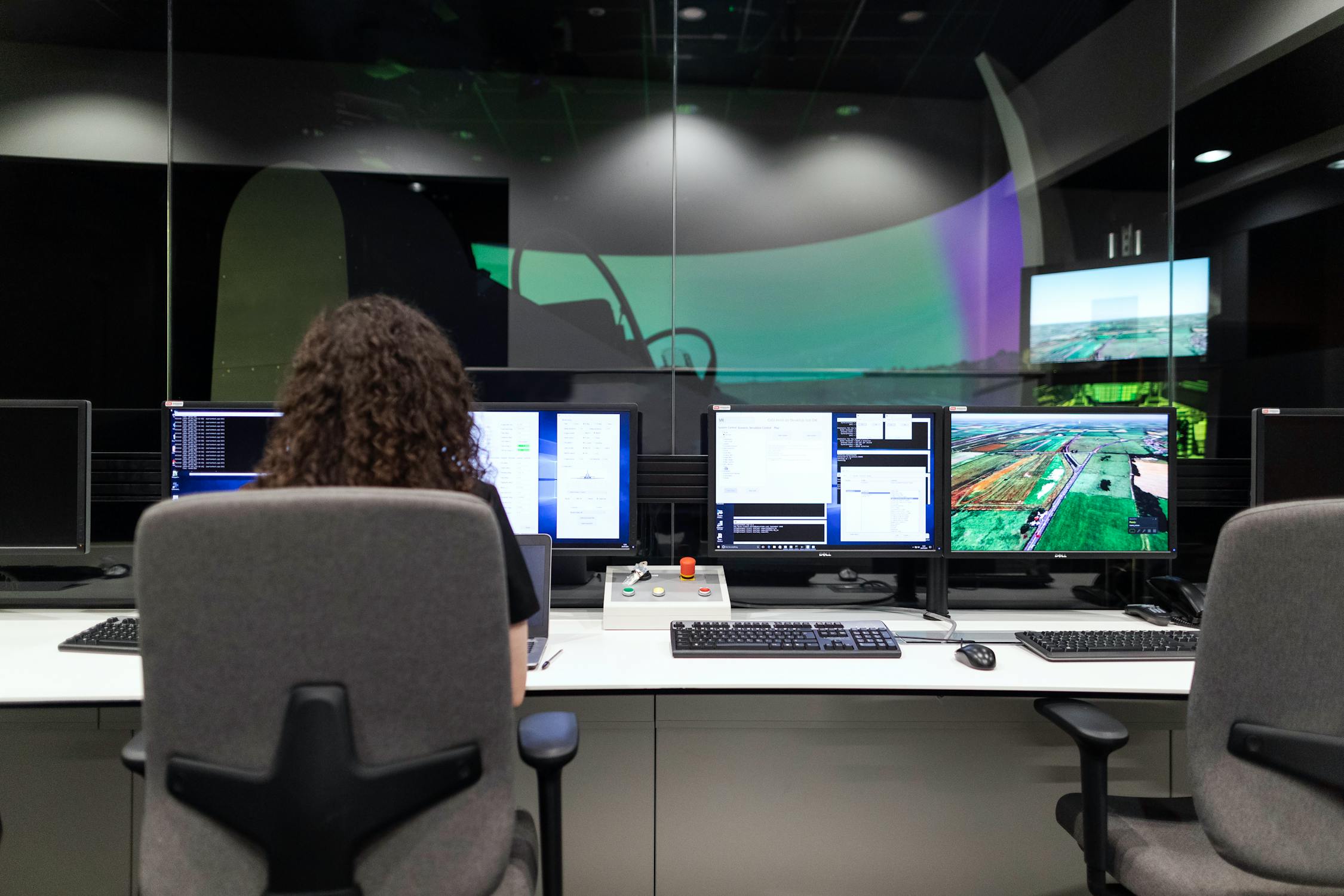
Thermal Analysis Methods
- CFD simulation for airflow optimization
- Thermal imaging for hotspot identification
- FEA for thermal stress analysis
- Real-time temperature monitoring system
Material Selection
- High thermal conductivity aluminum alloy (6061-T6)
- Advanced thermal interface materials
- Specialized surface treatments for heat dissipation
- Composite materials for thermal isolation
Design Optimizations
- Integrated heat sink features
- Optimized internal air channels
- Strategic component placement
- Enhanced surface area for heat dissipation
Implementation Process
Testing Procedures
- Thermal cycling tests (-20°C to 85°C)
- Environmental chamber testing
- Accelerated life testing
- EMC and safety certification testing
Deployment Strategy
- Phased rollout starting with pilot installations
- Comprehensive installation documentation
- Field technician training program
- Remote monitoring implementation
"The thermal management solution provided by ATI Engineers has exceeded our expectations. The significant reduction in operating temperature has not only improved reliability but also reduced our maintenance costs substantially."
Key Takeaways
The success of this project demonstrates several important principles for industrial equipment design:
- Early thermal analysis prevents costly field issues
- Integrated cooling features can outperform add-on solutions
- Material selection is crucial for thermal management
- Comprehensive testing validates design improvements
Technical Specifications
Key parameters of the optimized design
- Material
- Aluminum 6061-T6
- Surface Treatment
- Type III Anodizing
- Thermal Conductivity
- 167 W/m·K
- Max Operating Temp
- 85°C
- IP Rating
- IP66 (Dust/Water)
- NEMA Rating
- NEMA 4X
- Heat Dissipation
- 2500W at 40°C ambient
- Production Volume
- 1000 units/year
Ready to Optimize Your Design?
Let's discuss how we can improve your product's thermal performance.
Related Case Studies
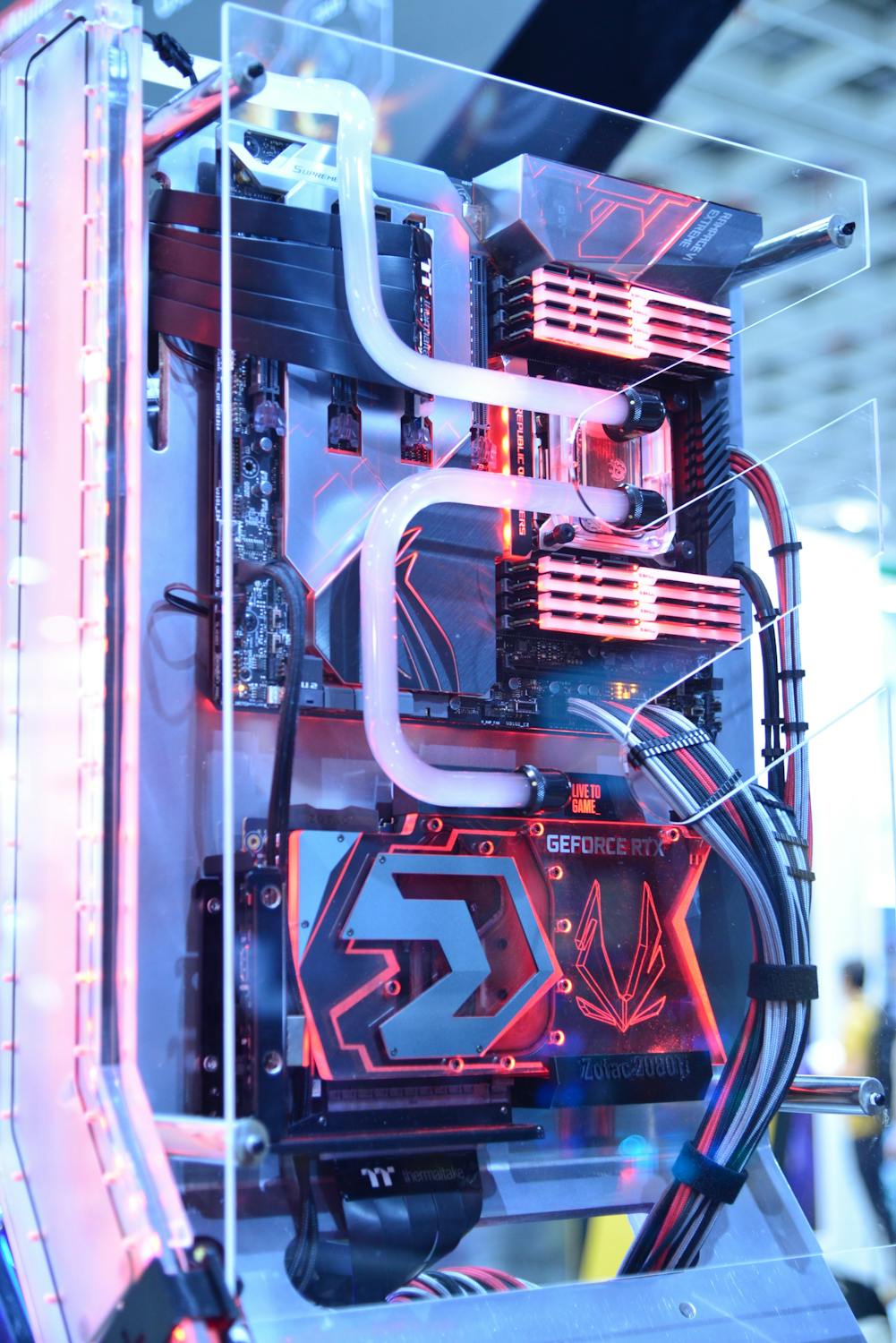
Consumer Electronics Enclosure
Water-resistant housing design for consumer electronics