Water-Resistant Innovation: Consumer Electronics Enclosure Design
Learn how we developed an innovative water-resistant enclosure design achieving IPX7 rating while optimizing production efficiency and maintaining aesthetic appeal.
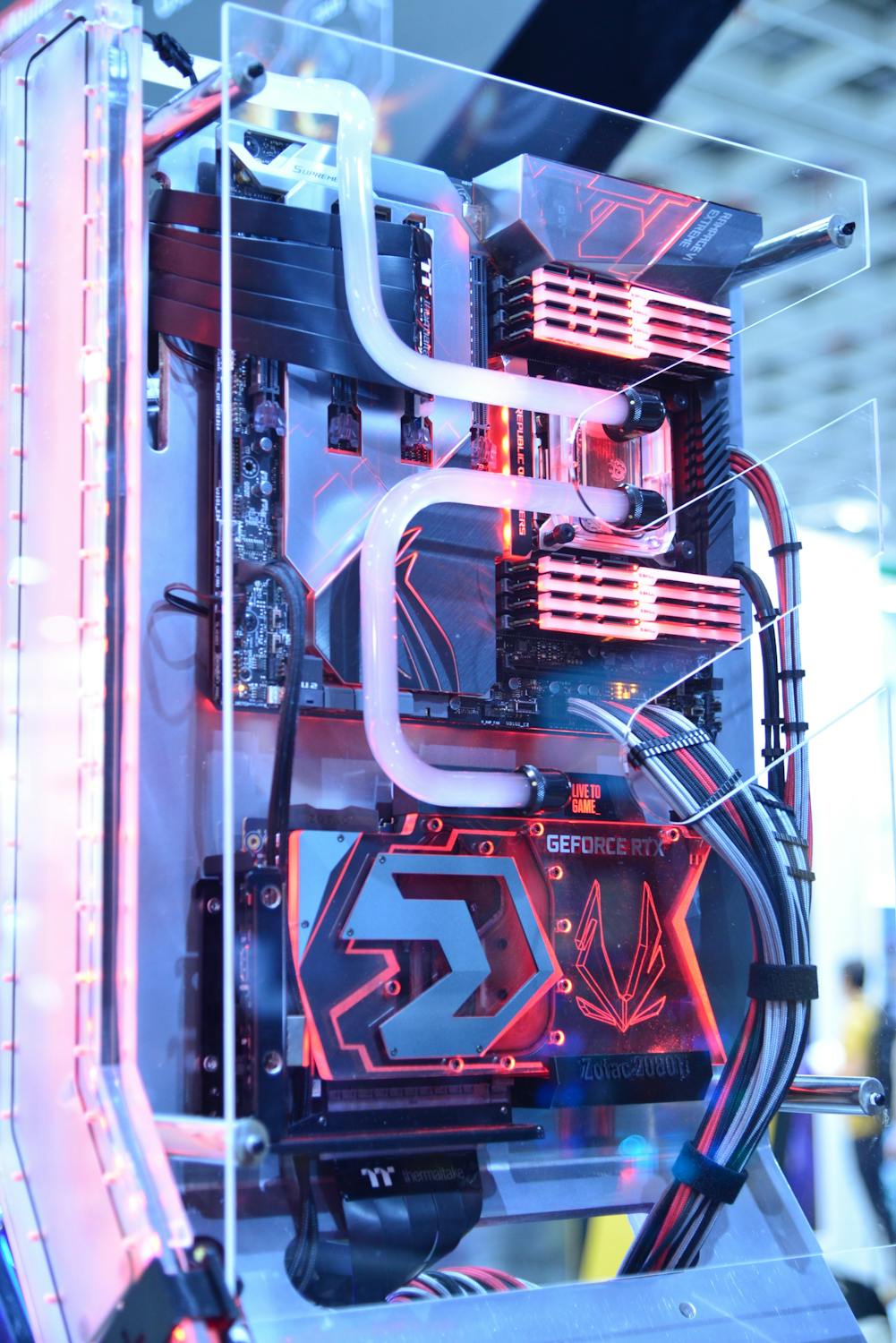
Key Achievements
IPX7
Water Resistance
Immersion up to 1m for 30 mins
15%
Cycle Time
Reduction in production time
8%
Material Cost
Optimization savings
Zero
Field Failures
Since launch
Project Background
A leading consumer electronics manufacturer approached us to develop a water-resistant enclosure for their next-generation portable device. The project required balancing multiple competing requirements:
- IPX7 water resistance rating requirement
- Premium look and feel with minimal seam lines
- Efficient heat dissipation for internal components
- High-volume production capability (500K units/year)
- Cost-effective design for competitive market positioning
Technical Challenges
Water Resistance Design
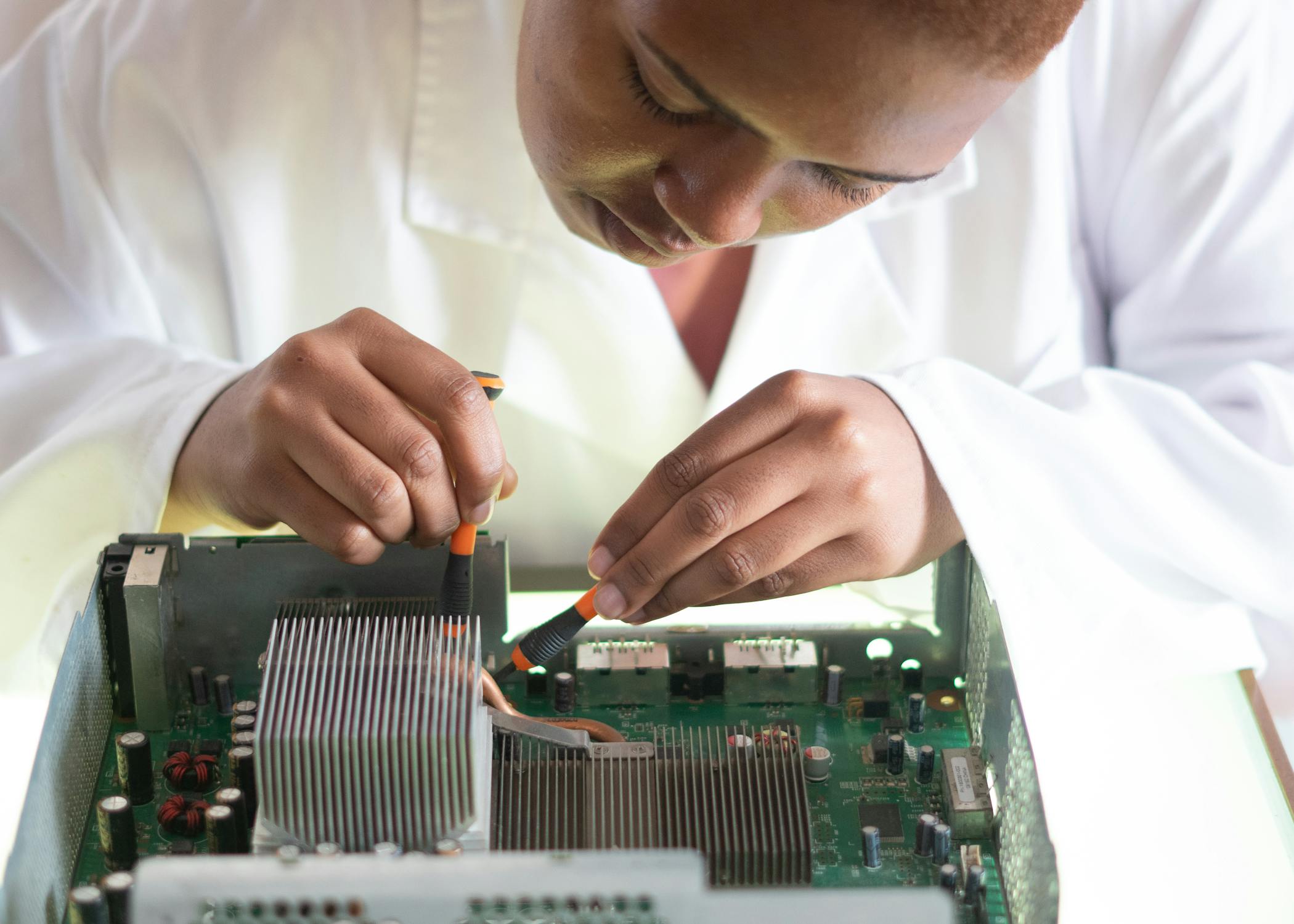
- Complex geometry requiring multiple seal interfaces
- Port protection while maintaining accessibility
- Material selection for long-term seal integrity
- Testing and validation procedures development
Thermal Management
- Heat dissipation through sealed enclosure
- Thermal interface material selection
- Airflow optimization within constraints
- Temperature monitoring system integration
Manufacturing Considerations
- Multi-shot molding process development
- Assembly automation requirements
- Quality control and testing procedures
- Production cycle time optimization
Solution Development
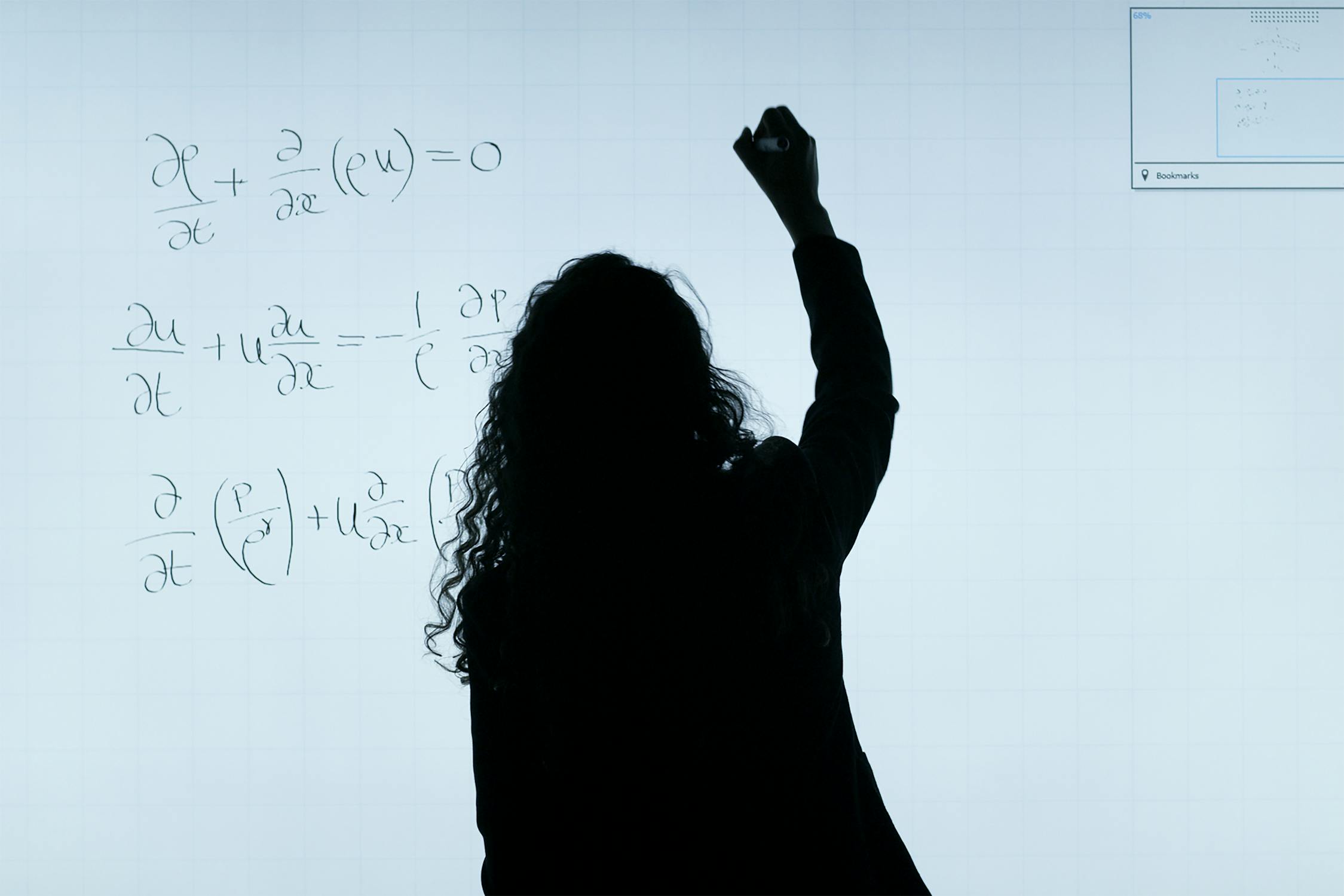
Sealing Technology
- Dual-shot LSR technology for primary seals
- Integrated snap-fit with secondary sealing
- Port covers with living hinges
- Pressure relief valve integration
Material Selection
- PC/ABS blend for structural components
- TPE overmold for grip and sealing
- Custom LSR formulation for durability
- Thermal interface materials optimization
Manufacturing Process
- Multi-cavity tool design with hot runners
- Automated assembly and testing stations
- In-line seal verification system
- Optimized cycle time through simulation
Implementation & Testing
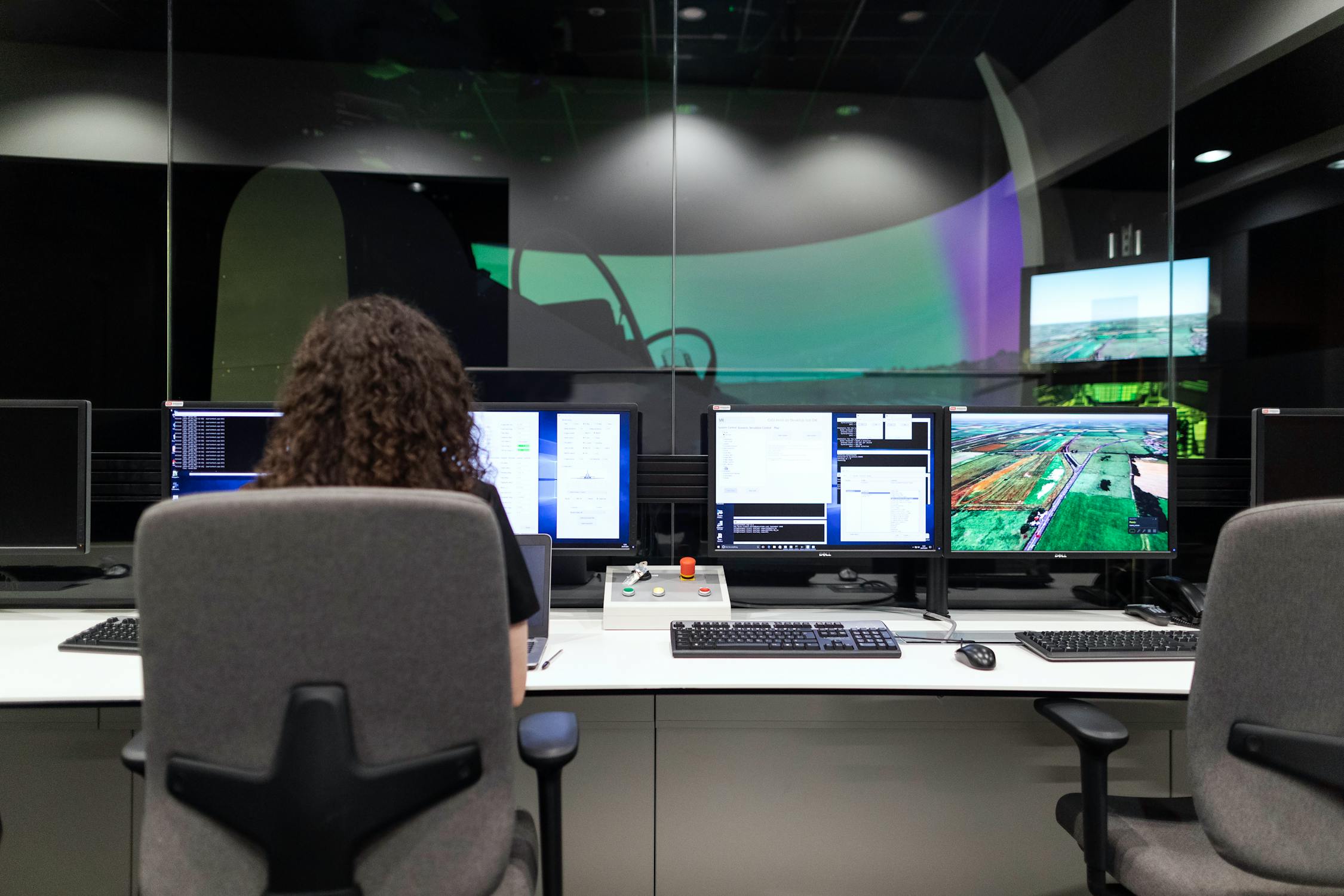
Rigorous testing and validation procedures were implemented to ensure design success:
- Environmental testing chamber validation
- Accelerated life cycle testing
- Drop and impact resistance verification
- Thermal performance monitoring
- Production line quality control procedures
Results & Impact
The project achieved all key objectives and established new benchmarks:
- Successful IPX7 certification achieved
- 15% reduction in production cycle time
- 8% material cost optimization
- Zero field failures reported since launch
- Positive user feedback on design and durability
"ATI Engineers delivered an exceptional solution that exceeded our expectations. The water-resistant design has become a key differentiator for our product in the market."
Technical Specifications
Detailed specifications of the final design
- Material
- PC/ABS with TPE Overmold
- Wall Thickness
- 1.5mm - 2.2mm
- Seal Design
- Dual-Shot LSR
- Assembly Method
- Snap-Fit with Secondary Seals
- Water Rating
- IPX7 Certified
- Temperature Range
- -20°C to +60°C
- Drop Rating
- MIL-STD-810G, 1.5m
- Production Volume
- 500K units/year
Ready to Waterproof Your Design?
Let's discuss how we can help protect your electronic products.