Streamlining Automotive Connector Assembly: A Study in Efficiency
Discover how we helped a tier-1 automotive supplier optimize their connector assembly process, reducing cycle time by 35% while significantly improving quality metrics.
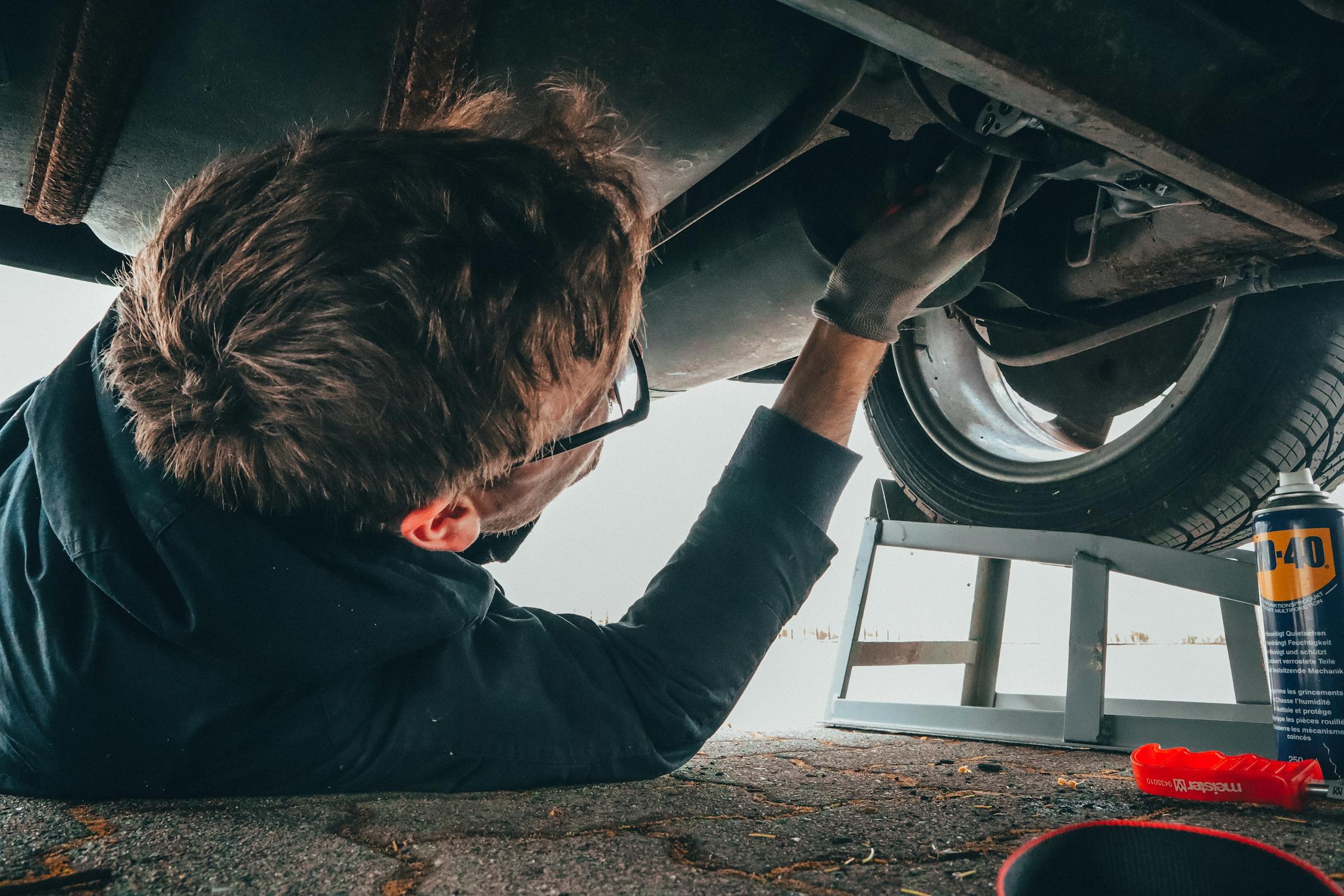
Key Achievements
35%
Assembly Time
Reduction in cycle time
80%
Defect Rate
Decrease in quality issues
12%
Material Cost
Total cost savings
2.5×
Maintenance
Extended tool life
Initial Challenges
The client faced multiple challenges in their high-volume automotive connector assembly process:
- Complex 12-step assembly process requiring precise alignment
- High defect rate (4.2%) due to terminal misalignment
- Frequent tool maintenance interrupting production
- Material waste from rejected assemblies
- Long cycle times impacting production targets
Solution Implementation
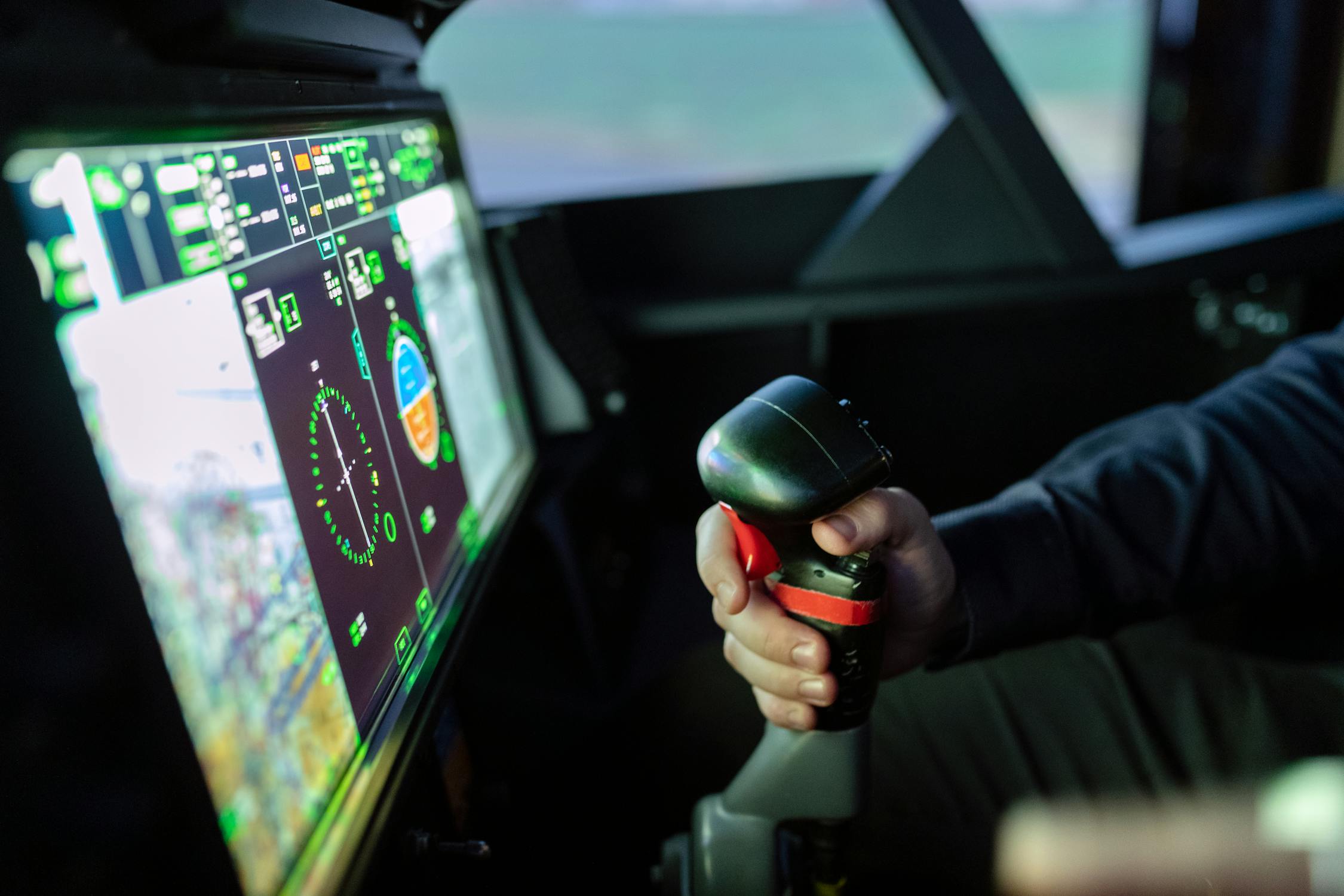
Our comprehensive solution addressed each challenge through systematic improvements:
Assembly Design Optimization
- Reduced assembly steps from 12 to 7 through component integration
- Implemented snap-fit features replacing manual fastening
- Added self-aligning features for foolproof assembly
Material Flow Improvements
- Redesigned feed system for continuous component delivery
- Implemented vision-guided robotic placement
- Optimized workstation layout reducing operator movement
Quality Control Integration
- Added in-line electrical testing at critical stages
- Implemented vision system for terminal alignment verification
- Developed real-time process monitoring dashboard
Tool Design Enhancements
- Upgraded to wear-resistant tool materials
- Implemented modular design for quick changeovers
- Added sensors for predictive maintenance
Results Analysis
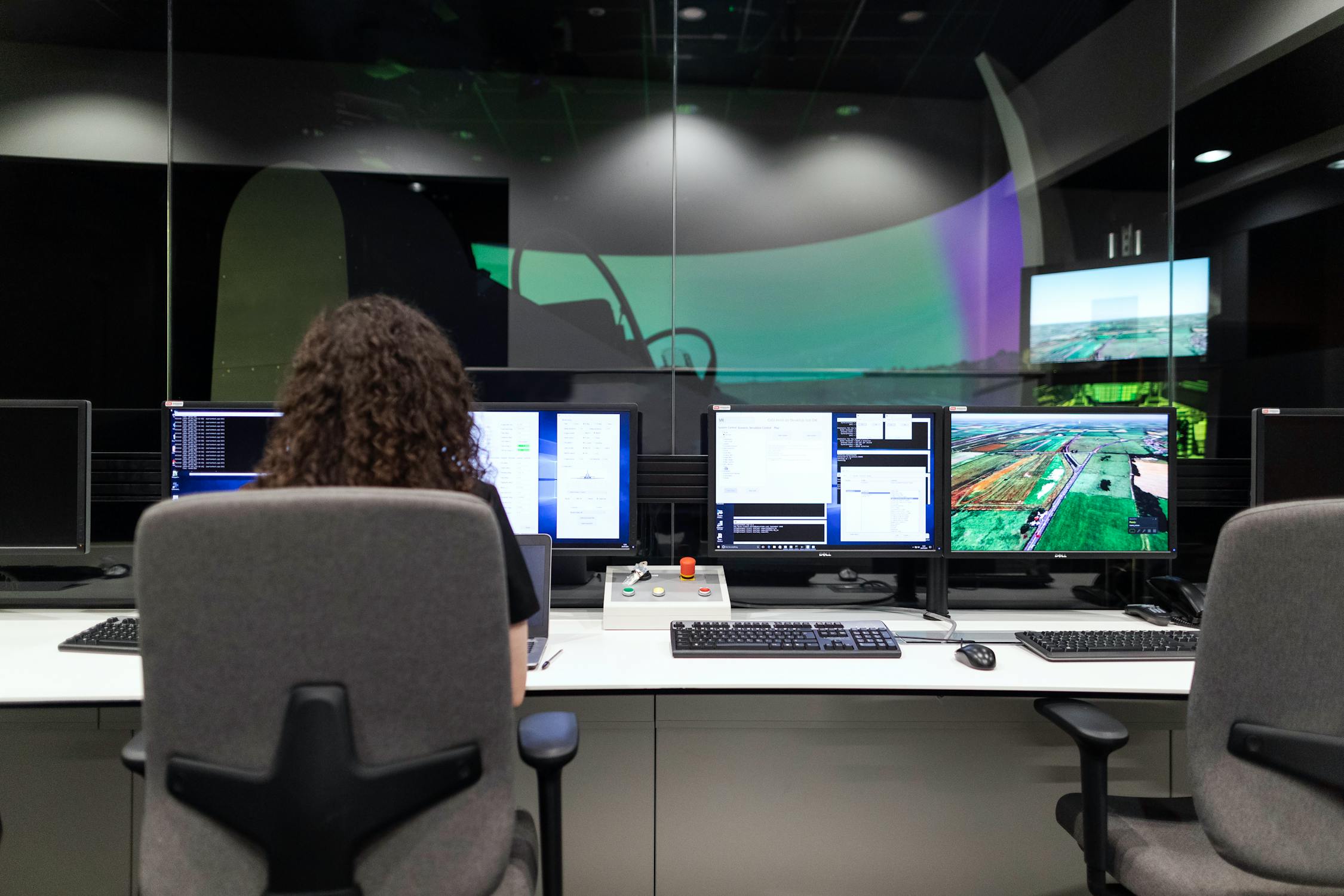
The implemented solutions delivered significant improvements across all key metrics:
Assembly Time Reduction
- Process simplification saved 22% of cycle time
- Automated material handling reduced time by 8%
- Improved ergonomics contributed 5% time savings
Defect Rate Improvement
- Terminal misalignment issues reduced by 95%
- Automated inspection caught 99.9% of defects
- First-pass yield increased from 95.8% to 99.2%
Material Cost Savings
- Reduced scrap rate saved 7% in material costs
- Component integration eliminated 3% of materials
- Improved handling reduced damage waste by 2%
"The process improvements implemented by ATI Engineers transformed our assembly operation. The reduction in cycle time and defects has significantly improved our competitiveness in the automotive market."
Future Recommendations
Based on the success of this project, we recommended several next steps:
- Expand automated inspection to other product lines
- Implement predictive maintenance system across facility
- Develop standardized workstation layouts for all assembly cells
- Create training program for operators on new processes
Technical Specifications
Key parameters of the optimized assembly
- Material
- Glass-Filled PBT/PET Blend
- Cavitation
- 4 Cavity Hot Runner
- Cycle Time
- 18 seconds
- Annual Volume
- 2.4M units
- Contact Rating
- 13A @ 12V DC
- Temperature Rating
- -40°C to +125°C
- IP Rating
- IP67 (Sealed)
- Mating Cycles
- >100 cycles
Ready to Optimize Your Assembly?
Let's discuss how we can improve your manufacturing efficiency.
Related Case Studies
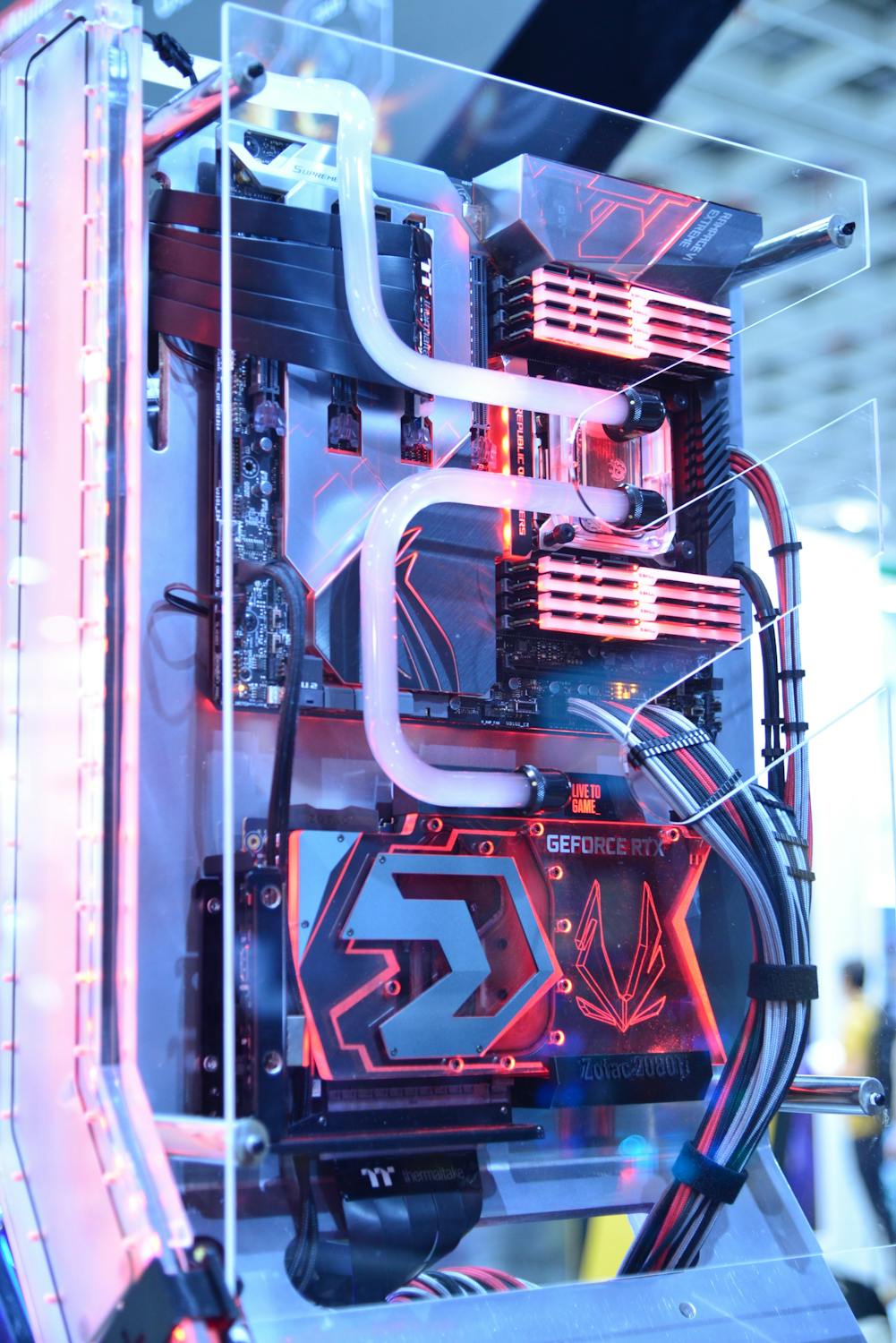
Consumer Electronics Enclosure
Water-resistant housing design for consumer electronics